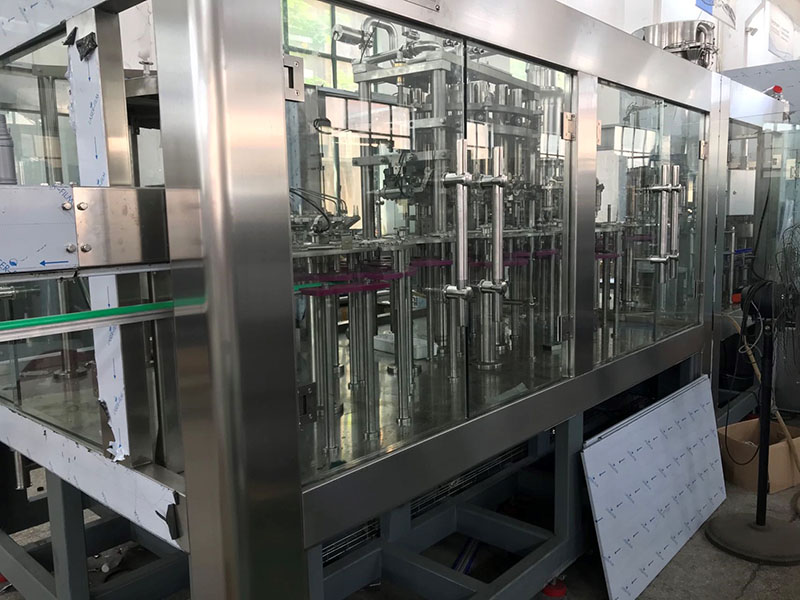
Main technical characteristics
(1)The Cap head has a constant torque device to ensure the Cap quality. (2)Adopt efficient Cap system, with perfect feeding Cap technology and protection device. (3)Change the bottle shape without the need to adjust the height of the equipment, replace the bottle star wheel can be realized, the operation is simple and convenient. (4)The filling system adopts card bottleneck and bottle feeding technology to avoid secondary contamination of bottle mouth. (5)Equipped with a perfect overload protection device, can effectively protect the safety of the machine and operators. (6)The control system has the functions of automatic water level control, insufficient Cap shortage detection, bottle flushing and self-stop and output counting. (7)The bottle washing system uses an efficient cleaning spray nozzle produced by the American spray company, which can be cleaned to every place in the bottle. (8)The main electrical components, electric control valves, frequency converter and so on are imported parts to ensure the excellent performance of the whole machine. (9)All the components of the gas circuit system are used in internationally known products. (10)The whole machine operation adopts advanced touch screen control, which can realize man-machine dialogue. (11)The NXGGF16-16-16-5 type PET bottle is pure water washing, plunger filling, plunger filling, sealing machine, absorbing the advanced technology of similar foreign products, with stable performance, safe and reliable. (12)The machine is compact structure, perfect control system, convenient operation, high degree of automation; (13)Using the air supply channel and into the bottle dial wheel direct connection technology, cancel the bottle supply screw and transport chain, simple and easy to change the bottle type. After the bottle enters the machine through the air supply channel, it is sent by the bottle inlet steel paddle wheel (card bottleneck mode) directly to the bottle flushing press for washingSterile water Washing Head
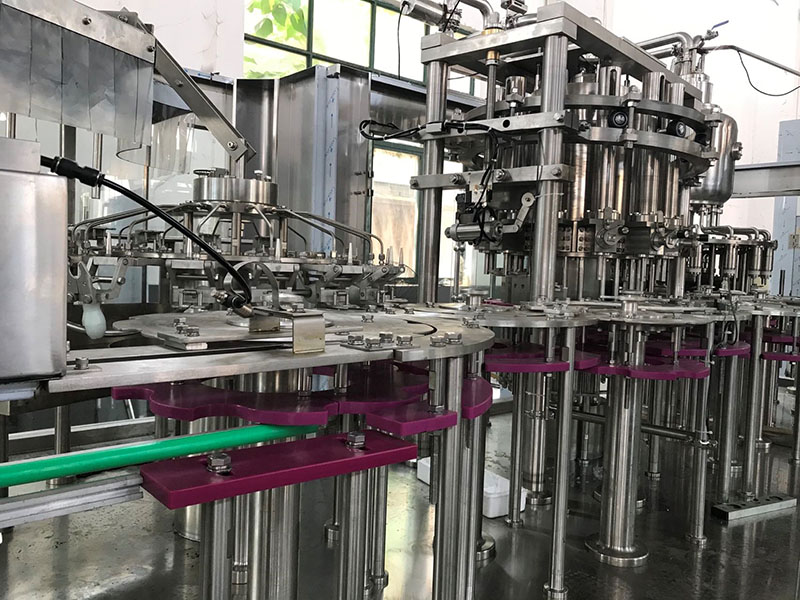
One Stage Pulp filling
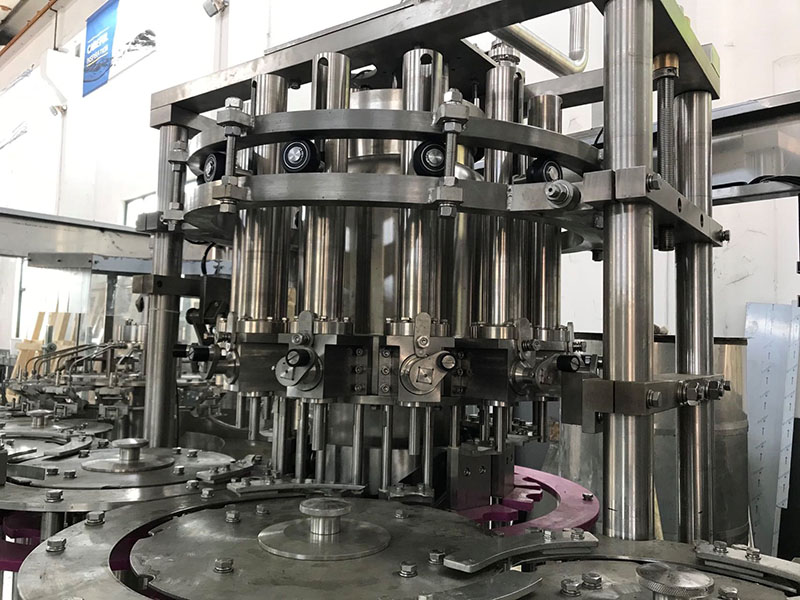
Second Stage concentrated Juice filling
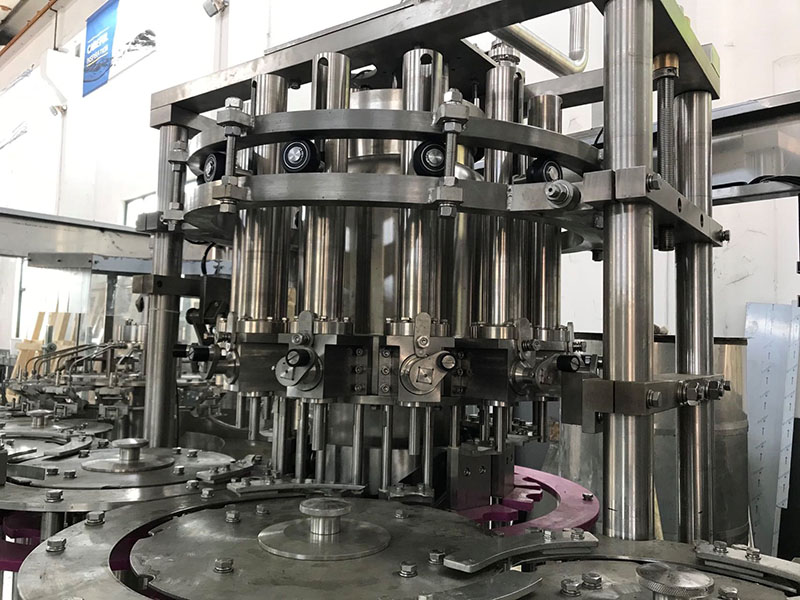
Capping Head
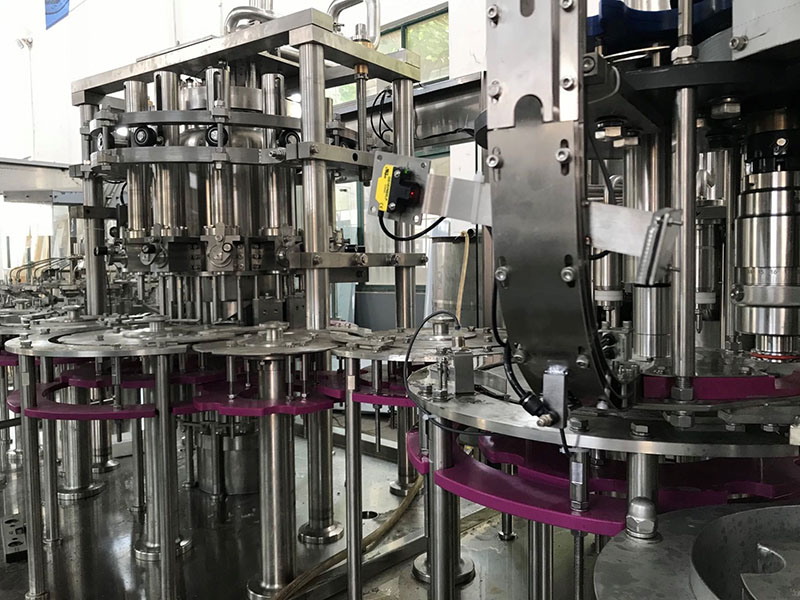
The Cap Arranging device
The Cap is transported to the Cap Arranging device through the Cap Loader. After the Cap enters the Cap device through the back Cap recovery device with the opening of the upward position. When the lid is opened down, the Cap will enter the back Cap tube through the back Cap recovery device and return to the Cap Arranging device, thus ensuring that the lid from the Cap Arranging device emerges. A photoelectric detection switch is provided in the Cap channel between the Cap Arranging Device and the Cap disinfection machine and the Cap disinfection and the main Machine, which controls the start and stop of the Cap device through the accumulation of the lid on the Cap channel.Main technical parameters
model | RXGGF16-16-16-5 |
The number of stations | Washing Head 16 Pulp filling Head 16 Juice filling Head 16 Capping Head 5 |
production capacity | 5500 bottles / hour (300ml / bottle, bottle mouth: 28) |
bleed pressure | 0.7MPa |
gas consumption | 1m3/min |
Bottle water pressure | 0.2-0.25MPa |
Water consumption of the bottle | 2.2 Tons / h |
Power of main motor | 3KW |
The power of the machine | 7.5KW |
external dimensions | 5080×2450×2700 |
The weight of the machine | 6000kg |